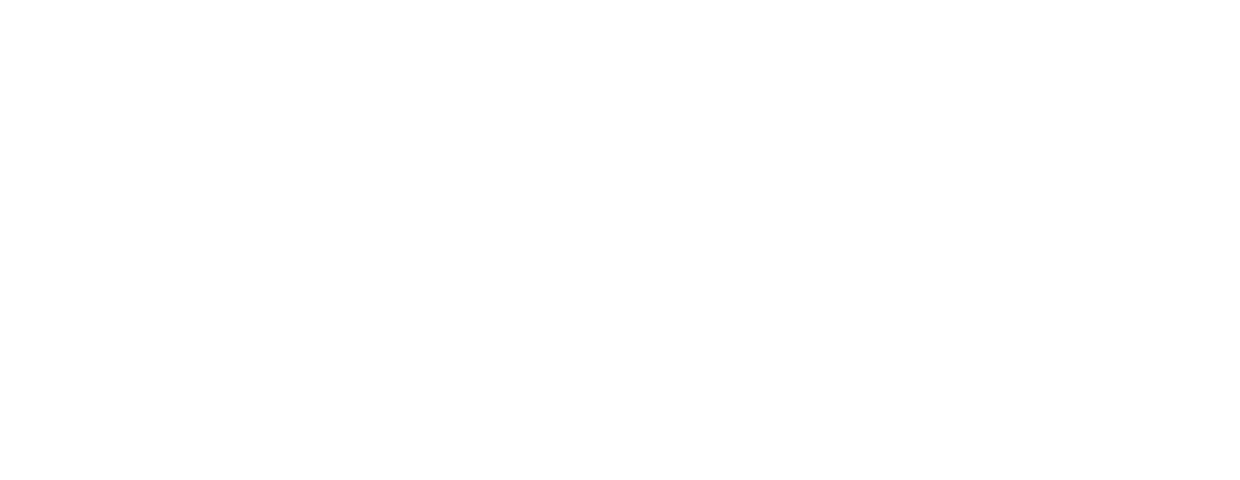
NSK Case Study

Application
Continuous Annealing
Process Line
Cost Savings: $399,296
The continuous annealing process line at a steelworks was experiencing unplanned stoppages. Downtime was averaging 17 hours annually at $23,488 per hour due to required heavy lifting machinery as well as additional maintenance personnel. NSK engineers performed analysis on the failed bearings and identified that both the bearing type and the sealing arrangement were inadequate for the application. The high load and low speed of the application were major factors impacting bearing performance. A multi-row sealed cylindrical roller bearing (for crane sheaves) was an ideal solution.
Key Facts
![]() |
Steel strip manufacturing process – multiple locations |
![]() |
High load and slow speed application |
![]() |
Inadequate bearing specification in original equipment design |
![]() |
Bearing failure due to contamination and improper lubrication |
![]() |
Lost production of 17 hours annually |
Continuous Annealing Process Line
Value Proposals
![]() |
Failure analysis revealed significant fatigue on the existing ball bearing |
![]() |
Crane sheave bearing unit with integral sealing arrangement proposed |
![]() |
Machine design review resulted in a modified housing design to accommodate bearing |
![]() |
Bearing condition analysis performed mid-trial demonstrated no indications of wear |
![]() |
Post-trial review showed no significant bearing damage |
![]() |
Bearing life was extended to more than 3 years |
Product Features
![]() |
Accommodates extremely high radial and axial loads |
![]() |
Advanced contact seal prevents grease leakage and ingress of water and external contaminants |
![]() |
Corrosion resistant phosphate coating permits use in a wide range of environments, including exposure to external environments |
![]() |
Simple re-lubrication – even during operation – with inner and outer ring lubrication holes and grooves |
![]() |
Bearings filled with Lithium Complex grease |
![]() |
Can be fitted with snap rings on the outer ring |

Cylindrical Roller
Bearings for Crane Sheaves
Cost-Savings Breakdown
Before | Cost | NSK Solution | Cost | |||
---|---|---|---|---|---|---|
![]() |
Lost production: more than 119 hours over 7 years due to bearing failure. Annual downtime: 17 hours X $23,488 | $399,296 | No lost production: Bearings in full operational condition after 3 years in service.Expected lifetime of the new NSK design: 5 years | $0 | ||
Total Costs | $399,296 | Total Costs | $0 |
Before | Cost | |
---|---|---|
![]() |
Lost production: more than 119 hours over 7 years due to bearing failure. Annual downtime: 17 hours X $23,488 | $399,296 |
Total Costs | $399,296 |
NSK Solution | Cost | |
---|---|---|
![]() |
No lost production: Bearings in full operational condition after 3 years in service. Expected lifetime of the new NSK design:
5 years |
$0 |
Total Costs | $0 |
Your Partner for Machine Optimization
Our AIP Added Value Program is based around a simple proposition: ‘improvement pays’. By working with you throughout the AIP Value Cycle, we will help you achieve improvements in machine reliability, productivity and performance, all of which carry a tangible and measurable cost benefit – and we have the tools to prove it! That’s what we mean by improvement pays.
