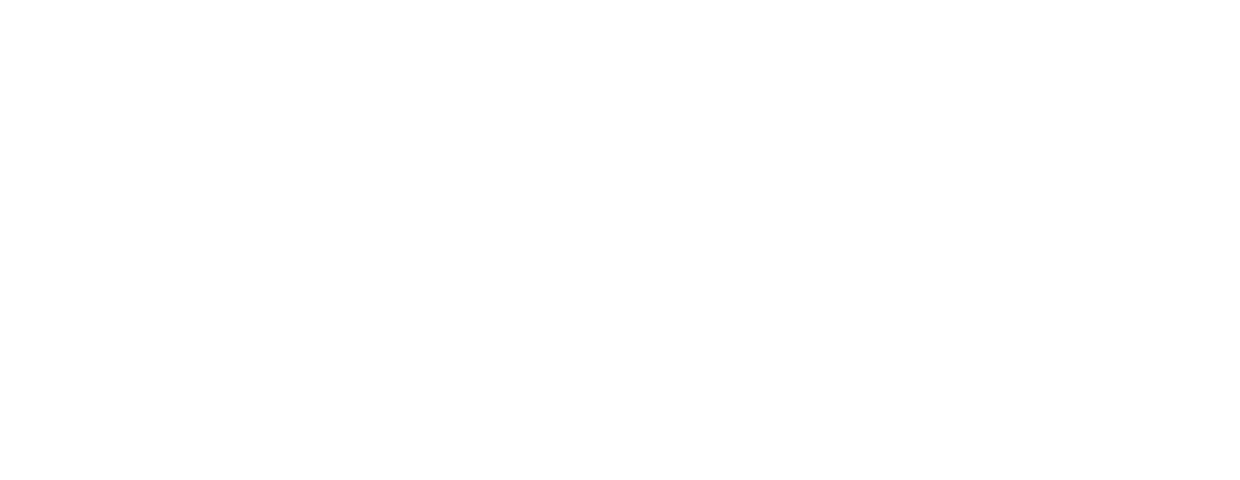
NSK Case Study
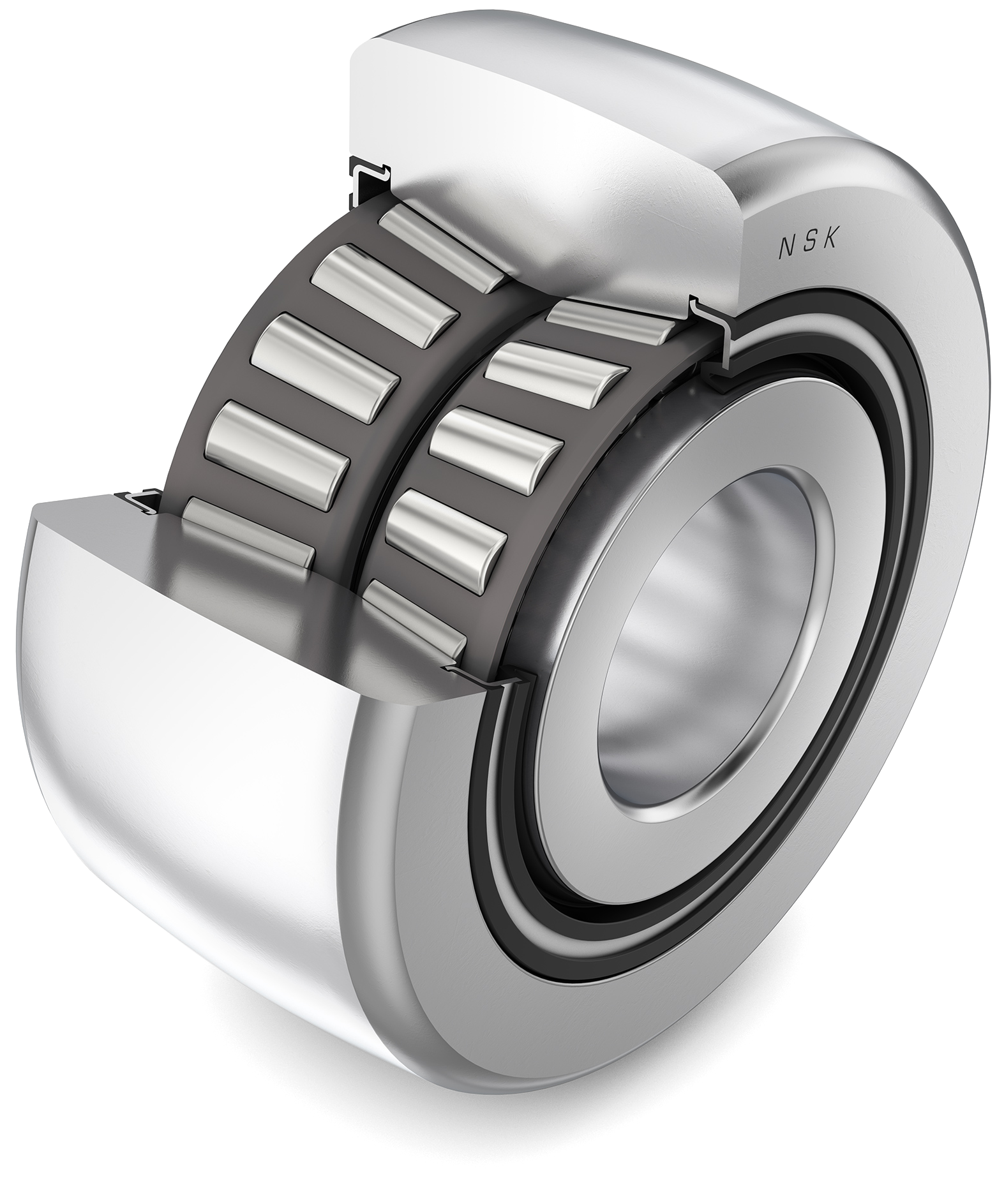
Application
Pipe Forming Roll
Cost Savings: $2,164,800
A large steel manufacturer wanted to achieve longer replacement intervals for the bearing solutions used in their pipe forming mill. The customer had been using a bearing arrangement consisting of 2 different competitor products: a double-row cylindrical along with a needle thrust bearing on each side of the roll. The average operating life for this bearing arrangement was 4 months before catastrophic failure of the needle roller bearing occurred, with components from the bearing becoming rolled into the pipe and creating marginal scrap. NSK approached the application with an original product design – a sealed-clean double-row tapered roller bearing unit capable of accommodating significantly higher axial and radial loads. This recommendation increased the bearing replacement interval threefold.
Key Facts
![]() |
Previous bearing arrangement running approximately 4 months before failure and replacement |
![]() |
Significant lost production |
![]() |
NSK solution: special design sealed double-row tapered roller bearing |
![]() |
Dramatically increased operating life |
![]() |
Reduced mill downtime |
![]() |
Significant cost savings for bearing replacement and maintenance |
Pipe Forming Roll
Value Proposals
![]() |
NSK engineers reviewed the application and operating conditions |
![]() |
Analysis revealed inadequacies of previous solution, and determined performance requirements of new product design |
![]() |
A special design sealed tapered roller bearing was produced, delivered and installed |
![]() |
The customer experienced significant increased bearing life, reduced maintenance intervals and associated cost, and dramatic savings in lost production due to frequent downtime |
Product Features
![]() |
Special design double-row tapered roller bearing |
![]() |
Accommodates high radial and axial loads |
![]() |
Integral seals provide advanced contamination resistance |
![]() |
Double-cup design with 2 cones and a cone spacer |
![]() |
Cone spacer is equipped with holes to facilitate efficient relubrication |
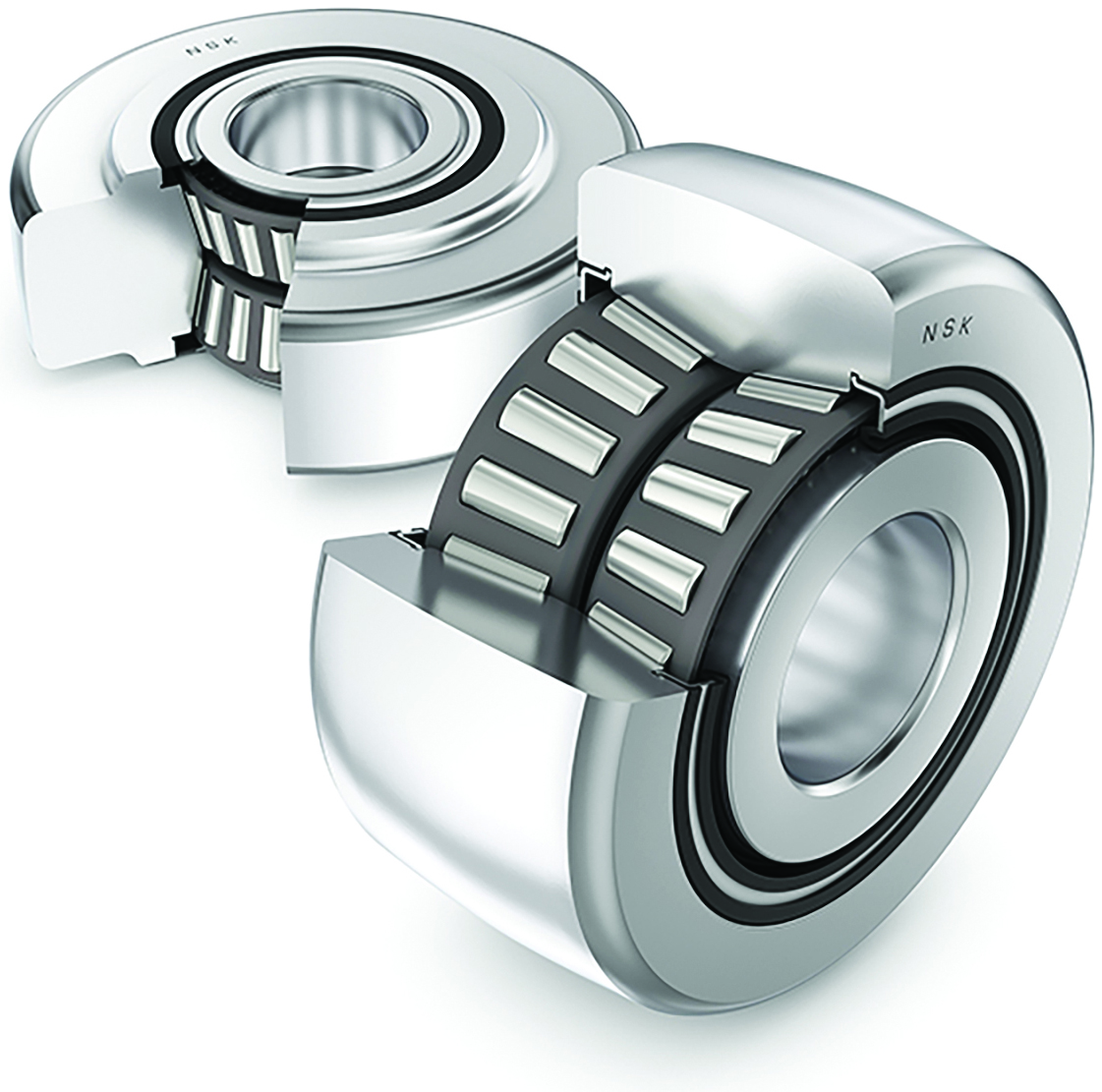
Double-Row Tapered
Roller Bearings
Cost-Savings Breakdown
Before | Cost | NSK Solution | Cost | |||
---|---|---|---|---|---|---|
![]() |
Lost Production | $2,769,250 | Lost Production | $692,300 | ||
![]() |
Bearing Replacement | $113,850 | Bearing Replacement | $28,450 | ||
![]() |
Maintenance | $3,300 | Maintenance | $850 | ||
Total Costs | $2,886,400 | Total Costs | $721,600 |
Before | Cost | |
---|---|---|
![]() |
Lost Production | $2,769,250 |
![]() |
Bearing Replacement | $113,850 |
![]() |
Maintenance | $3,300 |
Total Costs | $2,886,400 |
NSK Solution | Cost | |
---|---|---|
![]() |
Lost Production |
$692,300 |
![]() |
Bearing Replacement | $28,450 |
![]() |
Maintenance | $850 |
Total Costs | $721,600 |
Your Partner for Machine Optimization
Our AIP Added Value Program is based around a simple proposition: ‘improvement pays’. By working with you throughout the AIP Value Cycle, we will help you achieve improvements in machine reliability, productivity and performance, all of which carry a tangible and measurable cost benefit – and we have the tools to prove it! That’s what we mean by improvement pays.
